Pink Elephant launches Kanban e-learning course
So you’ve heard about the can-can, you may even be able to raise that leg yourself, but can you do the Kanban?
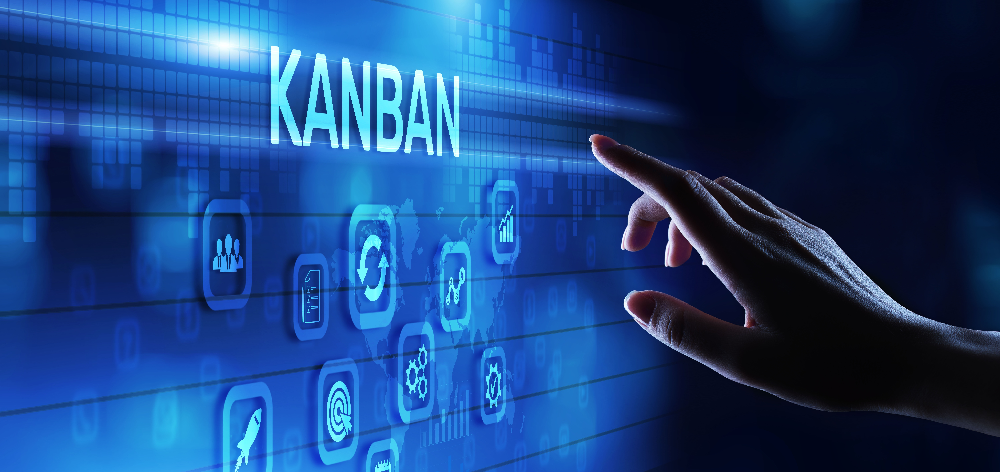
Pink Elephant launches Kanban e-learning course
The Japanese method (Kanban translates as ‘visual board’ or ‘sign’) optimises your company’s workflow through the simple but genius art of visualisation. Once mastered, your business capabilities will flourish and customer satisfaction will, consequently, skyrocket.
Sign up for Pink’s Kanban course here
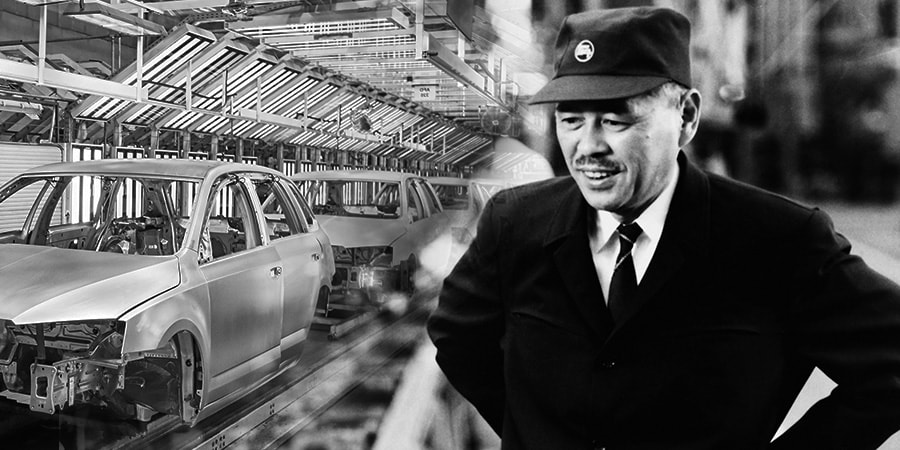
Scroll down below for Kanban’s six core practices.
Where does Kanban come from?
You, too, can learn the art of this method, which was devised in the 1940s by a Japanese industrial engineer and businessman by the name of Taiichi Ohno. He applied a just-in-time manufacturing system to optimise Toyota car manufacturing, known as the Toyota Production System.
“Wisdom is given equally to everybody. The point is whether one can exercise it.”
Taiichi Ohno
Get certified with Pink’s Kanban e-learning course
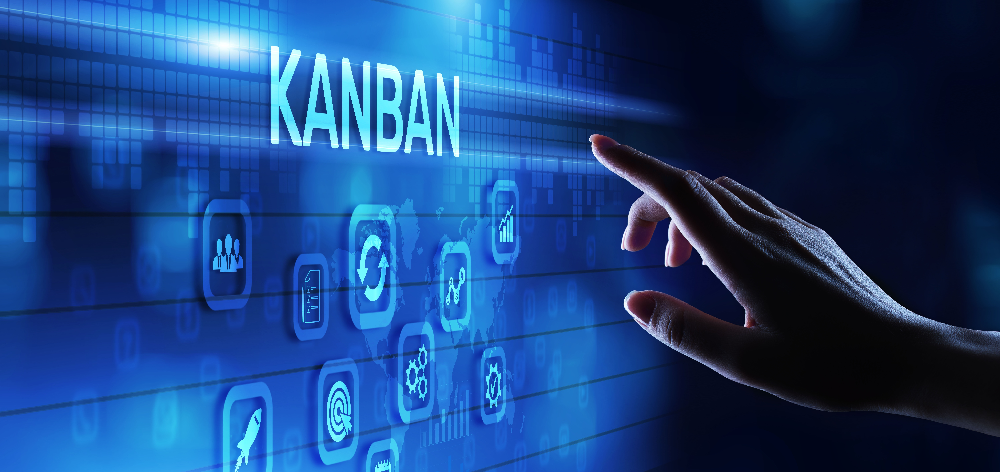
Pink Elephant is excited to launch one of the first Kanban Foundation® e-learning courses, certified by the exam institute EXIN.
Our Pink e-learning portal course will allow you to learn at your own speed and on any device, with interactive quizzes, learning materials and a trial exam to boost your chances of success.
The Kanban certification focuses on understanding the principles of Kanban and applying them in practice with the help of Kanban tools.
This course will help learners to describe the benefits and principles of Kanban and it will explain how workflows are optimised in practice through the use of Kanban tools. Moreover, the impact of Kanban culture in the organization and some areas of concern when scaling Kanban will be analysed.
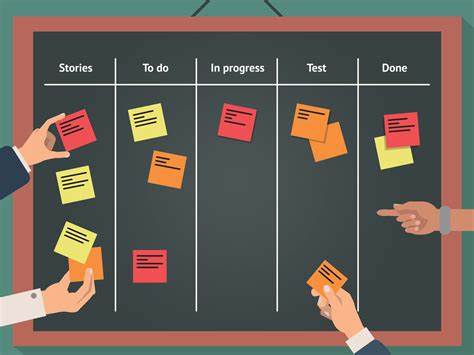
What are the six core practices of Kanban?
There are six core practices in maintaining a system with Kanban:
- Visualise the flow of work – One way in which this can be achieved is by using a kanban board. To ensure maximum efficiency, this visualisation should show where the commitment point (when a work item is allocated to a specific team) and the delivery point (when the work item is delivered to the customer) are in the process.
- Limit work-in-progress (WIP) – In limiting the work in progress and being guided by these limits to determine when to start new items, the completion of work items can be improved in both quality and quantity.
- Manage the flow – Kanban works at identifying stressors in your process to minimise lead times and improve predictability.
- Make process policies explicit – In making policies clear and explicit, processes are explained better than simply stating the different stages in the workflow.
- Implement feedback loops – To ensure significant progress and evolutionary change in a system, the feedback loops are essential.
- Improve collaboratively, evolve experimentally – The aim of Kanban is not to achieve a predefined goal but rather to constantly improve processes incrementally.
What are the key benefits of a Kanban course?
Some of the key benefits to be gained from this course include gaining theoretical and practical knowledge which can be applied to your job role immediately.
Additionally, the knowledge learned on this course is transferable with Kanban practices also present in Agile, Scrum, Lean and Sigma.
You can expect all the necessary resources and materials, as well as the official exam, to be included in the price of this new course.
Don’t delay and sign up for a Kanban course now!